[1] Palghat, S. L., Bhat, P. R., Trasad, V. A. (2021). Association Of Maternal Oral Health With The Oral Health Of The Child: An Observational Clinical Study. International Journal Of Scientific Research,10(9). [pdf]
Six Sigma
Six Sigma is a method that provides tools to improve the capabilities of business processes. This helps increase productivity and reduce variation in process leading to eliminating defects, improving the quality of service and products, employee productivity & morale, and finances & profits of the organization.
The main objective of six sigma methodology is to standardize processes so that the probability of errors is reduced. This is done using statistical quality process methods. A six sigma process is one in which 99.99966% of opportunities of a part of process is to be statistically free of defects.
The Six Sigma Methodology -DMAIC & DMADV
Six Sigma methodology mainly consists of two main concepts
- DMAIC– Define, Measure, Analyze, Improve, and Control
- DMADV– Define, Measure, Analyze, Design, and Verify
DMAIC is a data driven quality strategy that is useful when trying to improve an existing process, service or product. The DMAIC concept is a series of five steps that is used to
- understand or define what the problem is,
- then it is measured to receive existing data at unaltered state,
- once it has been measured the problem and data is analyzed to understand the root cause,
- after analyzing improvement strategies are developed to address the root cause,
- and lastly is to control the improvements and look for future improvements.
DMADV also known as Design For Six Sigma (DFSS) is a process methodology that is employed to design or re-design a process that does not exist. The DMADV also consists of five steps,
- first define what are the requirements of the project from the perspective of the patient/customer,
- then understand what are the relevant metrics to track and measure the requirements,
- analyze how can the goals be best achieved,
- after analyzing the data is used to design the new service or product,
- and finally in the verify phase it is checked if the end results meets or exceeds the customer requirements

Application of Six Sigma Methodology in Healthcare
Healthcare is mainly a service oriented industry which can be a hands-on process. This leads to high possibility of variations as compared to other industries. Six Sigma principles can be used to eliminate defects, variation in process leading to a more streamlined process, improving quality and less costly.
- Defect– defects in healthcare is defined as a factor that leads to patient dissatisfaction
- Define– what do the patient’s want? what are the customer expectations whether- patients, staff or payers? what is the objective of the identified problems or issues?
- Measure– converting the critical quality factors (CTQs), voice of the customer into measurable variables. These metrics can be divided into four groups: service level, service cost, customer satisfaction and clinical excellence.
- Analyze– the team identifies what are the causal factors (X’s) which are most likely to have an impact on the response variable (Y’s). If the causal factors are controllable and significantly influences the response variable then the results can be improved by controlling the causal factors (X’s). If the causal factors are uncontrollable then a new process should be created to reduce the variability. An example of a uncontrollable factor in healthcare is arrival rate of patients to the Emergency Department (ED).
- Improve– implement modifications to improve the process
- Control– monitor performance to maintain improvement by introducing new control measures and process metrics to drive behaviour and cultural changes in the organization
Some ways how Six Sigma has helped healthcare. Six Sigma has known to improve patient care by
- Reducing the number of variations by physicians, nurses, technicians by standardizing processes
- Improving lab turnaround times
- Improve patient appointment waiting times
- Improving patient outcomes
- Decreasing the number of steps in the supply chain
- Accelerating reimbursement for insurance claims
Six Sigma Tools & Techniques
Various tools and techniques are used in six sigma projects
SIX SIGMA TECHNIQUES | DESCRIPTION |
Brainstorming | Is done by assessing the given situation and gathered information, discussing about creative ideas and solutions. The main aim is to come up with multiple creative ideas and then narrow it down to feasible solutions. |
Root Cause Analysis/5 Why | This technique is done to reach to the root of the problem by questioning why the problem occurred 5 times. Solutions are constructed to address the root cause of the problem. |
Voice of Customer | Is the customer/ patient’s perspective, comments, requirements, expectations of the product or service under discussion. This is used to define our problem and identify the metrics to measure. |
The 5S system | Is used to create an organized environment improving efficiency of work. It consists of 5 steps- sort, set, shine, standardize and sustain. |
Benchmarking | It is a process that is used to compare the performance of the output (process, service, product) to a standard. This is done by interviewing, conducting site visits and documenting the performance and comparing the results to the set standard to understand the gaps. |
Kaizen | Is continuous improvement of processes, service or products by creating a standardized method, increasing efficiency and reducing waste. |
Poke-yoke/ Mistake Proofing | It is a method of taking steps to mistake proof a process. It starts with understanding the cause effect relationship of the defect followed by a remedy that prevents the defect from occurring. |
Value Stream Mapping | Is used to understand the information and material flow in a process. It is useful to identify potential areas of improvement leading to increased efficiency. |
SIX SIGMA TOOLS | DESCRIPTION |
Cause and Effect Analysis | Also known as fishbone /Ishikawa is used to show the potential causes of a particular event or issue. It also helps to understand root cause of the problem. |
Flow Chart | It lays out the various stages or steps within the process. It is helpful tool in standardizing a process. |
Pareto Chart | It is a graphing method that provides information on the frequency of defects and their cumulative impact. |
Histogram | Is an approximate representation of distribution of numerical data. It divides the range of values into intervals and group the values according to the intervals . |
Check Sheet | It is documentation of quantitative or qualitative data in real time at the location where the data is generated. |
Scatter Plot | Is a mathematical diagram that is used to display typically two variables for a set of data. It can be used either when one continuous variable is under the control of the experiment and the other depends on it or when both continuous variables are independent. |
Control Chart | It is a graph that is used to study how a process changes over time. These charts usually have a central line that represents the average, upper limit line and lower limit line. Historical data is used to plot these charts and the charts are used to understand the various patterns in existing data. |
A mix of these tools and techniques aid in understanding the existing process, identify areas that can be improved, develop solutions and implement improvement strategies driving organizations to achieve six sigma quality.
References
Value Stream Mapping
Value Stream Mapping also known as “Material & Information Flow Mapping”, is a lean management method that analyzes the current and future state for the series of events that takes a product or service from the beginning of the specific process until the end.
These value stream maps show the flow of both materials and information as they progress through the process. It is used to
- identify waste,
- reduce process cycle times, and
- implement process improvement
Value Stream Mapping(VSM) is a visual representation of the series of steps and information that is useful to understand the status of the process at a glance, while identifying areas of possible improvement. It is a type of process map that enables the leadership to see where the actual value is added in the process, allowing them to improve overall efficiency.
How to create a Value Stream Map (VSM)?
The main drive of value stream mapping in healthcare is to understand how value is delivered to the patients. For this it is necessary to understand what value means to the various stakeholders like patients, service users and carers along with those involved in the value stream.
Once the team has been created the next step is to map what is happening at the moment, the current state. Once the current state has been mapped the focus is shifted to mapping the future state which represents significant changes from the current state. Lastly, an implementation plan is developed to make the future state a reality.
Common system measurements that can viewed using VSM in healthcare:
- Cycle Time (CT)– the time that elapses from the time a patient finishes a point in the process to the time the next patient finishes the same point in the process
- Value Added Time (VA)– the time that actually adds value to the patient’s journey
- Changeover Time (CO)– the time taken for the patient to switch from one process to the next, commonly known as handoff time
- Number of People (NP)– needed to undertake a particular process
- Available Working Time (AT)– of staff involved in part of the process. It is the time that the staff are actually available i.e. the shift time minus the break time
- Lead Time (LT)– the time it takes a patient to move all the way through the process or value stream
“ Creating a VSM for the process of medication refill for a patient in a pharmacy”
Patient’s with long term or chronic diseases are commonly treated with medication. These medications although necessary for management of the disease for long periods of time, they are usually dispensed as smaller batches by the pharmacy.
Here is a typical process map when a patient visits a pharmacy for refill of medication.
A Value Stream Map (VSM) of the medication refill process provides a glimpse of the major steps in the process,
- With additional information on the flow of information;
- The steps which add value to the patient, steps that don’t add value to the patient and steps that don’t directly add value to the patient but are important;
- And information on different measurements of time in the process such as cycle time (CT), change over time (CO), lead time (LT) and value added time (VA)
Once the current state of the value stream is mapped, it can be used to identify potential areas of improvement. In this VSM three process steps can be modified to reduce the waiting time of the patient. Possible solutions to the identified improvement areas:
- Have an automated reminder prompt to the pharmacy’s order system of patient’s medication refill
- The order entry technician confirms the physician’s prescription order, initiates order, prints label
- If the patient requires doctor’s consultation before refill of medication a message is sent to the patient
- The patient is sent a message reminder to come to collect medication at the pharmacy
- The fill technician fills the medication, checks the order and keeps it ready before the patient arrives
If this protocol is adapted the patient arrives at the pharmacy, meets with order entry technician who takes the patient’s details, and the process continues from the pharmacist counting the medication and doing quality checks. This moves few steps which does not require the actual presence of the patient to before the patient arrives essentially reducing the total lead time.
What is the power of Value Stream Mapping?
The value stream map is useful during quality improvement to identify the wastes during the lean process, and identify the root cause of the problem . The process of VSM helps in identifying the issues and problems that add value perspective to the patient/consumer.
Quality improvement approaches start with defining the problem/issue, then measure, then analyze, improve and control which is commonly known as DMAIC framework as per the Six Sigma methodology.
Value Stream Mapping is tool that is mainly used to analyze the data to identify wastes in the system and the root causes. For example, the patient has to wait for a long time at the pharmacy. Using the value stream map it may be possible to understand that the problem is it takes too long for the fill technician to find the medication. On analyzing this further we can reach to the root cause of the problem, that is the medication is not stocked in a systematic manner. Now that the root cause is identified, the medication can be arranged using a Kanban 2-bin system improving overall efficiency.
References
Lean Healthcare
Lean Healthcare is the application of lean ideas in healthcare to minimize waste in every process, procedure, task through an ongoing system of improvement.
The concept of Lean was introduced by the Toyota Production System (TPS). Lean was based on five principles
What is lean according to the Toyota Way?
The Toyota Production System (TPS) is based on two main concepts:
- “Just-in-Time” which means only make what is needed, when it is needed and in the amount that is needed.
- This concept mainly relates to having a takt time( which is understanding how long will I need to make and assemble products so as to match my demand),
- have a continuous flow such that I have minimal inventory and
- have a system driven by a pull system ( which is production and delivery is based on demand)
- ” Jidoka” which means autonomation.
- This means that when an error is detected in the production line, the line is stopped, the abnormality is inspected, it is then fixed or corrected, and a root cause analysis is done and finally counter-measures are introduced.
- This ensures that the quality of the products are not compromised.
These two main concepts are the pillars to achieve the goals of delivering high quality products at low cost and the shortest lead time.
How can the concepts of lean be translated to healthcare?
The Lean concept introduced by Toyota can be adopted into healthcare.
- The “Just-in-Time” can be interpreted as providing the right service in the right amount at the right time in the right place; essentially eliminating undertreatment/ overtreatment and underuse/overuse of resources. Another aspect is to ensure continuous flow of supplies that will make sure the use of fresh supplies and prevent expiration of medical supplies.
- The other would be “Built in Quality“. This is important as it checks for quality issues. Any quality issue that is detected is assessed, analysed, corrected and immediately taken care of.
- Currently most of the healthcare system works on the push system wherein supply is not determined by demand. The lean method favours the use of a pull system wherein supply is determined by demand.
- Use of 5S and Visual Control – The 5S are Sort, Set in order, Standardize, Shine, & Sustain. The lean Visual Control uses color coded, easy to identify arrangements or instruction charts that can convey information at a glance improving patient care and help standardize control measures.
- Value Stream Mapping is another improvement method that lays out the processes and flow in a visual format.
What are the wastes in relation to healthcare?
Wastes in healthcare, is when efforts or expenses are expended but the patient or the consumer of healthcare is not receiving the benefits from the system in value to their expenses/efforts.
Type of Waste | Examples in Healthcare |
Defect |
|
Overproduction |
|
Waiting |
|
Unused Talent |
|
Transportation |
|
Inventory |
|
Motion |
|
Extra Processing |
|
Applicability of Lean Thinking in Healthcare
The adoption of lean thinking in healthcare can improve the patient care experience, organizing existing processes , improving provider experience, can improve finances by spending only on what is required and prevent stalled resources immobilising money and infrastructure.
While lean improvement strategies implemented can be beneficial, there are some important points to consider for the success for a lean project. Lean thinking is a continuous process and has very little room for error. An organization using lean thinking has to embrace a culture and ensure that all their employees and processes are working according to the prescribed way at regular intervals for it to work.
There have been quite a few healthcare organizations that have started using lean methods. One of the first hospitals to adopt the TPS was Virginia Mason Hospital in 2002.
References-
Kanban in Healthcare – a Way of the Future?
Clinical Microsystem Theory
A healthcare Clinical Microsystem is a group of professional who work together on a regular basis, or as needed to provide care to discrete populations of people.

The idea is based on the fact that smaller teams of professionals can work interdependently to provide quality patient care experience. The essential elements of the microsystem include patients, clinicians and support staff, information and information technology and the care processes.
What is Microsystems Thinking?
Microsystems thinking was introduced by statistician and consultant Dr. Deming and business school professor James Byron Quinn. This concept makes some organisational assumptions
- Bigger systems (macrosystems) are made of smaller systems.
- These smaller systems (microsystems) produce quality, safety, and cost outcomes at the front line of care
- Ultimately the outcome of the macrosystem can be no better than the microsystems of which is it composed.
A successful microsystem has good leadership that is distributed to the front line staff, staff which is able to empower improvement, have a patient centred approach in the improvement and a way to measure the performance of the system
How to assess the effectiveness of clinical microsystems?
The effectiveness of a clinical microsystem can be assessed using the 5 P’s of clinical microsystem
How can the microsystems approach be used in healthcare?
It is necessary to understand the clinical microsystem at the process level. At the process level it provides a conceptual and practical framework for approaching organizational learning and delivery of care.
The clinical outcome of care consists of the core processes ( the basic work that involves patient care) and supporting processes ( that makes the core processes functional and operational) that would be required to provide care. The process can be detailed by using process mapping tools. Laying out the process can be used to identify potential areas of improvement on the system that is producing the processes and outcomes.
The microsystem does not focus exclusively on outcomes; rather gives comparable attention to process and structure, to the linkages among them, and to how they interact to respond to meet the needs of the patient population.
Here is an example of a process map to understand a microsystem designed to provide cardiovascular surgery care for children.
The power of such maps is that it can be used to analysed to generate improvement ideas like:
- What is the goal of the process?
- Is the process working like it should?
- Are there any obvious redundancies or complexities?
- How different is the current process from the ideal process?
- What are the various factions within the larger group, and how does this division support/ hinder more effective processing of patient care?
- What are the workarounds to the proscribed process?
Let us look at another example of service and information flow within the microsystem. This diagram shows the core process flow of patients in a microsystem and how planned services and planned care is designed to meet the individual patient needs.
References:
-
Understanding the complexity of redesigning care around the clinical microsystem
-
S.A.F.E. Toolkit Module 1 – Translating quality improvement into action
- Microsystems in Health Care: Part 4. Planning Patient-Centered Care
Human Centered Design
Human Centered Design(HCD) is a concept of developing systems and processes with the focus of the human in the center. The HCD develops frameworks while always keeping the perspective of the human in view while developing solutions.
A Human Centered Design in the healthcare setting would be developed with the “Patient” in the center, and problems are solved by developing systems, frameworks or protocols leading to favourable outcomes for the patient.
How to create a Human Centered Design?
Creating a Human Centered Design involves
- Discovering who will the design benefit, what problems entail the consumer;
- Define the problem and understand what can be done;
- Design a process or product or system such that it benefits the consumer;
- Prototype & Test the design;
- Plan & Implement
“Re-imagine the experience of receiving preventive and wellness care“
Our Goal-As a group we began to deliberate what do we want different in the experience of receiving primary care. Our idea of a redefined experience from a primary care visit was to focus on the preventive aspect of wellness.
Our Question-How to maximize the opportunity of inculcating the concept of healthy living and make access to education on healthy living available?
Conception of the idea-Address the disease at its roots. This meant improving facilities and access to information on common health conditions, their risks, how to prevent these diseases, general information on how to maintain physical and mental well being and any other health or lifestyle questions that may arise. Improving health education can help patients to live a healthier lifestyle and decrease the onset of disease and visiting the doctor. After thoughtful deliberation we agreed on our redefined design.
” A casual, community space where patients can receive education and resources from a primary care physician or health professional, without an appointment”
This serves as an inviting space where patients are free to learn about health related concerns from professionals while socialising with like minded people. Health education is also offered by putting up posters, pamphlets and advertising at different parts of the hospital as well as the city.
Other approaches to redefined primary care experience?
The idea of redefining the primary care experience sparked different aspects of the challenge among other peers.
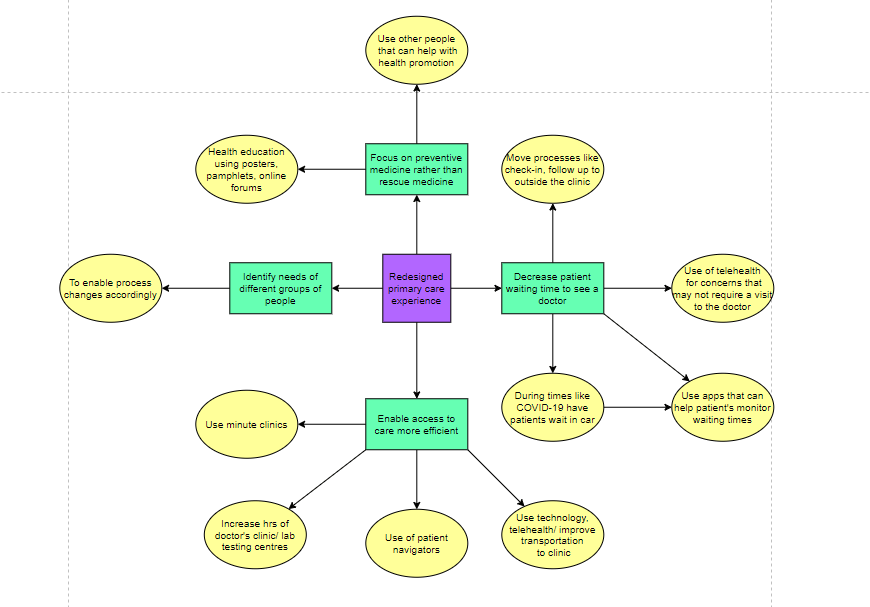
Yellow- Proposed ideas/ solutions
Power of the Human/Patient Centered Design (HCD)
The same design challenge was presented to all of us, yet the different groups seems to have approached it differently while keeping the essence of preventive wellness of the patient in mind.
Potential of HCD– The HCD is a useful tool that can be used to view the problem/situation from the view of the consumer/ patient where the ultimate design improves the intended audience experience.
Limitations of HCD– The HCD is more effective when a group or team of people are involved compared to when done individually or a smaller group.
Applications of HCD– HCD can be used in a multitude of situations. It is applicable in any industry or organisation that provides a service or product. Some areas in the healthcare industry that can use the Human Centered Design are
- Hospital facility– A patient centred approach can be used to improve any particular aspect of their existing process or system
- Medical device companies– The HCD concept can be used when designing a device which may be intended to use by the patients or the doctors/ medical staff
- Pharmaceutical companies– The Patient Centric Design concept is used when producing new medications, where the intend of any new drug will be to have less adverse and side effect for the patient
Modified Patient Centered Design
In our previous design model we did not include some aspects of preventive wellness. With taking inspiration and ideas from the work presented by other groups, I would modify our original design to include aspects of
- Reducing waiting time to see the doctor by using
- Online check-in which can move the pre-appointment paperwork,
- Patient is redirected to health education professional after doctor’s visit to ensure that patient is well informed about their health condition and answer any questions that a patient might have
- Improved navigation or access to healthcare system with the help of a patient navigator
The idea of a Patient Centered Design will include a team of professionals that work together to facilitate an outcome that is patient centric. These different teams of professionals will constitute a clinical microsystem.
About Me
Welcome,
I am Swati Lakshmi Palghat, a current Graduate student in Healthcare Systems Engineering at Lehigh University. With having some experience and when looking from the perspective of a healthcare provider I view and understand the healthcare system as a medium of providing services to improve health outcomes. As a healthcare systems engineer I will be able to examine and improve systems and process designs with an aim to improve efficiency, reduce errors, improve access and the overall quality of healthcare.
This website provides a brief overview of various tools and concepts that I will use with a systems approach to improve the overall quality of healthcare.